The following is a detailed introduction to immersion flange electric heating tubes:
Structure and Principle
Structure: The immersion type flange electric heating tube is mainly composed of U-shaped tubular electric heating elements, flange covers, junction boxes, etc. Install electric heating wires into seamless metal tubes, fill the gaps with magnesium oxide powder with good thermal conductivity and insulation, and shrink the tubes. Then, install multiple such heating tubes on the flange cover through welding or fastening devices.
Principle: When the electric heating tube is connected to the power supply, the heating wire generates heat, which is uniformly conducted to the metal tube through magnesium oxide powder, and then transferred to the heated medium by the metal tube.
Characteristic
High power and efficiency: using bundled tubular electric heating elements, small size, high power, fast thermal response, high comprehensive thermal efficiency, can quickly transfer heat to the heated medium.
Easy to install: The overall structure is compact, stable, and does not require a bracket for installation. The flange connection method enables it to be easily installed on various containers or equipment, and can be disassembled as a whole for easy replacement and maintenance.
Wide applicability: It can be used in explosion-proof or ordinary places, with explosion-proof levels up to Class IIB and C, and a pressure resistance of up to 20MPa. It can adapt to heating various liquids and acid-base salts, and can also be used for heating and melting low melting point metals.
Safe and reliable: Combination flange heating tubes mostly use argon arc welding to connect the heating tube to the flange, with good sealing and no leakage. At the same time, it has multiple safety protection measures such as overheating protection and leakage protection. When the heating element exceeds the temperature or the liquid level is low, the interlocking protection device will immediately cut off the heating power supply to prevent the heating element from burning out.
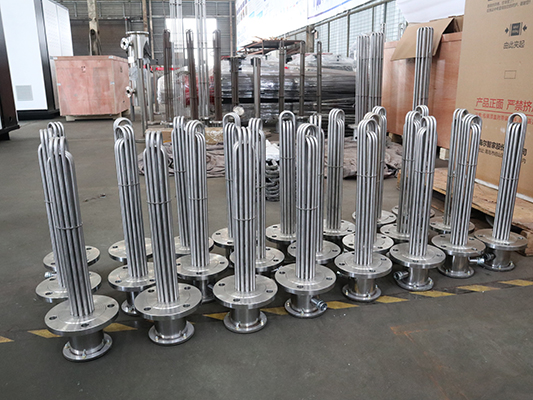
Application area
Petrochemical industry: used for heating and insulation of petroleum and chemical raw materials in various storage tanks, reaction vessels, pipelines, etc., to ensure that materials are reacted and transported at appropriate temperatures during the process.
Food and beverage industry: Heating raw materials, finished products, etc. in the food processing process, such as sterilization heating of milk and juice, and heating of fermentation broth in the brewing process.
Mechanical industry: Used for lubricating systems of mechanical equipment, heating oil in hydraulic systems, ensuring the viscosity and fluidity of oil, and ensuring the normal operation of equipment.
Power industry: can be used for circulating water heating, deaerator heating, etc. in power plants to improve the efficiency and safety of the power production process.
Selection and Installation
Selection: Choose the appropriate power, diameter, length, and material of the heating tube based on factors such as the type of heated medium, temperature requirements, flow rate, and container size. At the same time, it is also necessary to consider whether the working environment has special requirements for explosion prevention, corrosion prevention, etc.
Installation:
Before installation, ensure that the heating tube matches the power supply, control system, and other equipment. Check the appearance of the heating tube for damage and whether the insulation resistance meets the requirements.
During installation, the heating part of the heating tube must be completely immersed in the heating medium to avoid air burning. The wiring lead out part should be exposed outside the insulation layer of the heater or outside the heater to prevent overheating and damage.
When using flange connection, it is necessary to ensure that the flange surface is flat, the sealing gasket is installed correctly, the bolts are evenly tightened to prevent leakage.
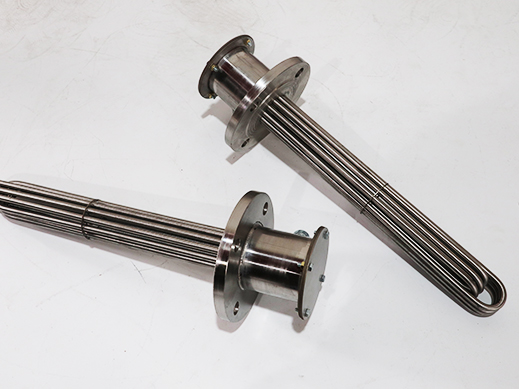
Usage and maintenance
Regular cleaning: Clean the heating tube at regular intervals to remove accumulated dust, scale, and carbon deposits on the surface, ensuring the heating effect. When cleaning, first cut off the power and wait for the heating tube to cool down, then use a soft cloth or brush for cleaning.
Inspection and tightening: Regularly check the wiring terminals of the heating tube to ensure that the nuts are tightened and prevent loosening. At the same time, check the part of the heating tube in contact with the medium for leaks and corrosion.
Power and voltage inspection: Regularly check the power supply voltage to ensure it is within the rated range and avoid damage to the heating tube caused by excessively high or low voltage.
Post time: Feb-20-2025