1. Working process and principle
The electric heating oil furnace mainly converts electrical energy into thermal energy through electric heating elements (such as electric heating tubes). These electric heating elements are installed inside the heating chamber of the thermal oil furnace. When the power is turned on, the heat transfer oil around the heating element absorbs heat and the temperature rises. The heated heat transfer oil is transported to the jacket or coil of the reaction vessel through a circulation pump. Heat is transferred to the materials inside the reactor through thermal conduction, causing the temperature of the materials to rise and completing the heating process. Afterwards, the heat transfer oil with reduced temperature will return to the electric heating heat transfer oil furnace for reheating, and this cycle will continue to provide heat to the reaction kettle.
2. Advantages:
Clean and environmentally friendly: The electric heating heat transfer oil furnace will not produce combustion exhaust gas during operation, which is very beneficial for some places with high air quality requirements, such as laboratories, clean workshops, and reaction kettle heating. For example, in the research and development laboratories of pharmaceutical companies, the use of electrically heated thermal oil furnaces can avoid the interference of combustion products on drug composition analysis and synthesis reactions, and will not produce greenhouse gases and harmful gases such as carbon dioxide and sulfur dioxide, which meets environmental protection requirements.
High precision temperature control: Electric heating can achieve more precise temperature regulation. Through advanced temperature control instruments, the temperature of the heat transfer oil can be controlled within a very small fluctuation range, generally achieving an accuracy of ± 1 ℃ or even higher. In the heating of reaction vessels in the field of fine chemical engineering, high-precision temperature control is crucial for ensuring consistency in product quality and performance.
Easy installation: The structure of the electric heating heat transfer oil furnace is relatively simple, and does not require complex burners, fuel supply systems, and ventilation systems like oil or gas heat transfer oil furnaces. For some small businesses or temporary heating projects with limited space, the installation of electric heating thermal oil furnaces next to the reaction kettle is more convenient, saving a lot of installation space and time.
Good safety performance: The electric heating heat transfer oil furnace has no open flames, reducing fire hazards. Meanwhile, the system is usually equipped with various safety protection devices, such as overheat protection, leakage protection, etc. When the temperature of the heat transfer oil exceeds the set upper limit of the safe temperature, the overheat protection device will automatically cut off the power supply to prevent the heat transfer oil from overheating, decomposing, or even catching fire; The leakage protection device can promptly cut off the circuit in case of leakage, ensuring the safety of operators.
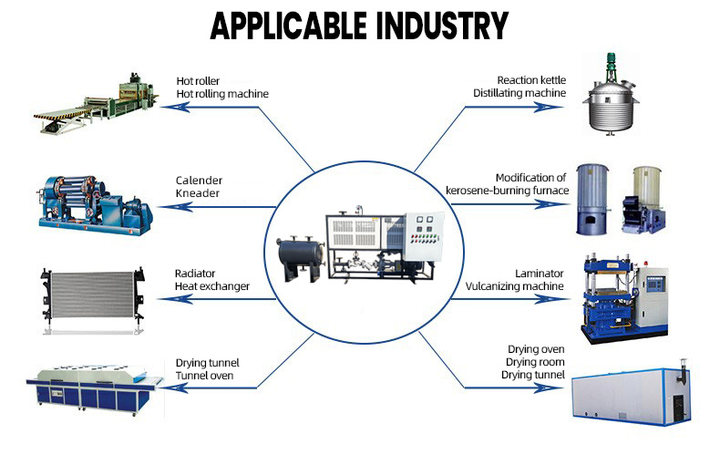
3. Application:
Chemical industry: In chemical synthesis reactions, such as producing high-purity organosilicon compounds, the reaction temperature is strictly required and impurities cannot be mixed in during the reaction process. Electric heating thermal oil furnace can provide a stable heat source, and its clean heating method does not introduce combustion impurities, ensuring the purity of the product. And the temperature can be controlled according to the reaction stage, such as controlling the temperature between 150-200 ℃ in the synthesis stage of organosilicon monomers and 200-300 ℃ in the polymerization stage.
Pharmaceutical industry: For the synthesis reaction of active ingredients in drugs, small temperature changes may affect the quality and efficacy of the drugs. Electric heating thermal oil furnace can meet the high-precision temperature control requirements of pharmaceutical reaction vessels. For example, in the heating of reaction vessels used in the production of anti-cancer drugs, temperature control can ensure the correctness of drug molecular structure and improve drug efficacy. At the same time, the environmental characteristics of the electric heating and heat transfer oil furnace also comply with the strict environmental standards of the pharmaceutical industry.
Food industry: In the synthesis and processing of food additives, such as the production of emulsifiers, thickeners, etc., reaction kettle heating is used. The clean heating method of electric heating thermal oil furnace can avoid harmful substances generated by combustion from contaminating food raw materials, ensuring the safety of food. And the heating temperature can be controlled, for example, in the heating of the reaction kettle for producing gelatin, by controlling the temperature within an appropriate range (such as 40-60 ℃), the quality and performance of gelatin can be guaranteed.
Post time: Dec-20-2024